Expert Light Weight Aluminum Spreading Solutions: Your Ultimate Guide
In the realm of manufacturing and design, the significance of light weight aluminum spreading solutions can not be overemphasized. From elaborate elements for aerospace applications to resilient parts for automobile industries, the convenience of light weight aluminum casting procedures supplies a broad variety of opportunities. Recognizing the nuances of various spreading techniques, browsing the complexities of quality assurance, and picking the appropriate solution supplier are just a couple of elements to take into consideration. As we embark on this exploration of expert light weight aluminum casting services, we will discover essential understandings that can elevate your jobs to brand-new elevations of accuracy and effectiveness.
Advantages of Light Weight Aluminum Spreading Provider
Light weight aluminum casting solutions supply a cost-effective and reliable technique for making high-grade steel elements. Among the crucial benefits of utilizing light weight aluminum spreading solutions is the adaptability it supplies in creating complex and complicated forms that might be challenging to produce making use of various other making techniques. The process enables for the manufacturing of get rid of slim walls, fine details, and smooth surfaces, making it perfect for a vast array of markets such as automobile, aerospace, and electronics.
Furthermore, aluminum casting solutions provide outstanding dimensional accuracy and uniformity, making certain that each component satisfies the called for specs. This integrity is vital for sectors where precision and harmony are vital. Furthermore, light weight aluminum is a lightweight material with high strength-to-weight proportion, making it an optimal option for applications where weight reduction is crucial without jeopardizing on longevity.
Additionally, light weight aluminum casting is a very scalable manufacturing procedure, with the ability of generating little to huge batches of parts effectively. This scalability makes it an economical option for both prototyping and automation, supplying flexibility to adapt to differing production needs. Overall, the benefits of aluminum spreading services make it a favored option for sectors seeking high-quality, affordable steel parts.
Sorts Of Light Weight Aluminum Spreading Procedures
Given the varied benefits that aluminum casting solutions offer, it is necessary to understand the various sorts of procedures associated with casting aluminum parts. Aluminum casting procedures are generally categorized into 2 primary kinds: expendable mold and mildew spreading and irreversible mold casting.
Expendable mold casting consists of approaches like sand spreading, financial investment casting, and plaster mold spreading. Investment spreading, likewise known as lost-wax spreading, is liked for detailed styles and high accuracy.
Long-term mold and mildew spreading entails processes like die casting and irreversible mold and mildew casting. Recognizing these different types of aluminum spreading procedures is essential for picking the most appropriate method for certain job requirements.
Variables to Think About When Picking a Provider
When choosing a solution supplier for light weight aluminum casting solutions, what vital elements should be taken into consideration to make sure a successful partnership? One crucial variable to evaluate is the company's experience and competence in light weight aluminum casting.

Top Quality Control Procedures in Aluminum Spreading

In addition, executing standard procedures and methods for quality control helps in lessening errors and discrepancies during spreading. Normal calibration of equipment and devices is essential to guarantee exact dimensions and casting specifications are fulfilled. Quality control steps additionally entail comprehensive screening of the chemical make-up and mechanical residential properties of the aluminum product before and after casting to validate its honesty and adherence to needed standards.
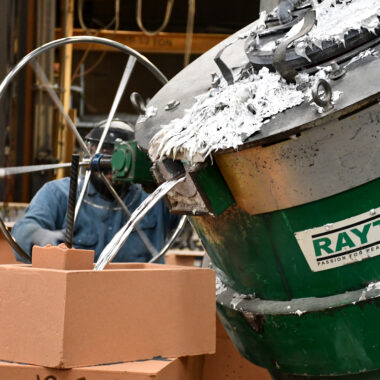
Tips for Successful Aluminum Casting Projects
Making sure the success of light weight aluminum spreading jobs depends heavily on executing critical guidelines to optimize the casting process and enhance overall task end results. To accomplish this, it is essential to start by very carefully developing the mold and mildew to fulfill the specific demands of the project - casting aluminum. The mold and mildew layout must consider factors such as material circulation, cooling rates, and possible problems to make sure a top quality final item
In addition, picking the ideal light weight aluminum alloy is paramount. Different alloys have differing residential properties that can considerably impact the casting procedure and the last item's features. Understanding the unique residential properties of each alloy and picking one of the most suitable one for the project can cause improved outcomes.
Additionally, keeping proper spreading temperatures and making certain constant monitoring throughout the procedure is important. check out this site Temperature variants can impact the top quality of the spreadings, so it is important to closely monitor and manage these criteria.
Finally, post-casting processes such as warm therapy and surface ending up need to not be overlooked. These actions can additionally boost the mechanical residential or commercial properties and appearances of the last aluminum castings, adding to the total success of the project.
Final Thought
In verdict, aluminum spreading services provide numerous advantages and come in various procedures. By carrying out appropriate quality control actions and adhering to expert tips, successful light weight content aluminum casting projects can be attained.
Expendable mold casting includes methods like sand spreading, financial investment casting, and plaster mold and mildew casting (casting aluminum). Financial investment spreading, additionally known as lost-wax casting, is preferred for intricate styles and high accuracy.Long-term mold casting includes procedures like die spreading and long-term mold and mildew spreading.When choosing a service provider for light weight aluminum casting solutions, what essential elements should be thought about to make certain an effective partnership?Making sure the success of light weight aluminum spreading projects depends heavily on applying strategic standards to maximize the spreading procedure and enhance general task results